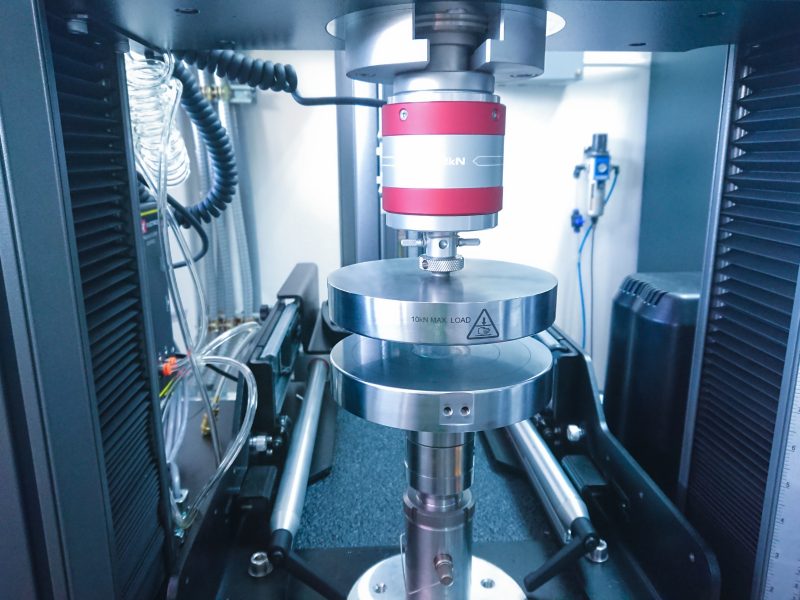
Do you need your injection molded part to withstand Thor’s Hammer?… Well maybe not… But there are design considerations to help molded parts hold up to the wear and tear of daily use even in industrial settings. Primary factors engineers should consider include material selection, design of ribs, fillets and radii.
When impact resistance is required, the result of the notched IZOD impact test is the top consideration in resin selection. This test is performed to determine the amount of energy plastic can absorb before permanent deformation occurs. Some of the most impact resistant plastics are Acrylonitrile butadiene styrene (ABS), High-density polyethylene (HDPE), Polycarbonate (PC), Polyamide-imide (PAI), and High impact polystyrene (HIPS). Selection is not limited to the previously listed materials, as various resins can be impact modified to mitigate brittleness issues.
Material choice is important, however poorly designed parts can crack even if molded in the most impact resistant material. Notches and sharp corners should be avoided and parts should be designed with the goal of distributing load over large areas with flexibility where impact loads are expected. Properly designed ribs are helpful to increase rigidity, but engineers must be careful to avoid defects on the surface of the part. Critical factors for rib design include the use of radii at the corners and proper thickness, as sink marks will form if the rib base is too thick. Sharp corners create stress, therefore it is important to design corners with appropriate fillet radius to improve impact resistance. The radius of the fillet should be about 0.5 to 0.6 times the thickness of the wall section to reduce stress concentration. See the illustration below to better understand these concepts.
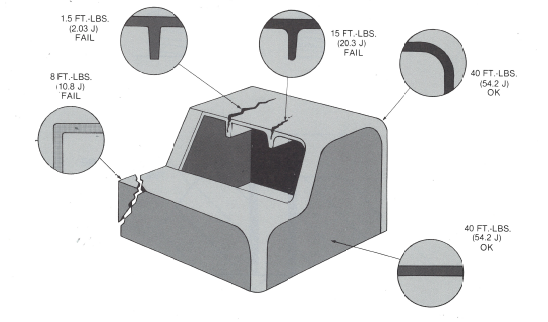
I.F. Associates, Inc., has earned a reputation for quality and reliability over 45 years in business. We do our best to assist customers to ensure quality of injection molded parts and longevity of the molds used to produce them. We welcome customers to take advantage of our experience to solve technical challenges and improve design for moldability.
Click here to Contact Us for review and quotation of your next project or Click here to email your information.